ОБЩАЯ ХАРАКТЕРИСТИКА НЕПРЕРЫВНОЙ РАЗЛИВКИ
1. Разновидности и преимуществаспособа
Непрерывную разливку или литье вместо разливки стали в изложницы начали применять в последние 30 лет. В настоящее время этим способом разливают около 83% выплавляемой в мире стали, а в развитых капиталистических странах до 97% производимой стали.
Наиболее распространен способ непрерывной разливки, заключающийся в том, что жидкую сталь непрерыно заливают в водоохлаждаемую изложницу без дна — кристаллизатор, из нижней части которого вытягивают затвердевший по периферии слиток с жидкой сердцевиной. Далее слиток движется через зону вторичного охлаждения, где полностью затвердевает, после чего его разрезают на куски определенной длины. Основа этого способа — вытягивание формирующегося слитка из кристаллизатора, т.е. скольжение слитка по его стенкам с возникновением при этом значительных сил трения, что является определенным недостатком способа; из-за трения возникают разрывы затвердевающей оболочки движущегося слитка, что ограничивает скорость разливки. Этим способом в настоящее время получают преимущественно литые заготовки (слитки) толщиной от 100—150 до 250—300 мм, что позволило ликвидировать два энергоемких этапа металлургического производства— прокатку на обжимных станах и нагрев слитков перед этой прокаткой в нагревательных колодцах.
Интенсивно ведутся исследования по дальнейшему совершенствованию и разработке новых оборудования и технологии непрерывной разливки. Одно из важных разрабатываемых направлений — получение литых заготовок значительно меньшей толщины, чем внастоящее время (например, тонких слябов и полос) и заготовок, приближающихся по сечению к конечному прокату, что позвлит применять для их прокатки станы меньшей мощности, обеспечивая экономию энергозатрат.
Другим важным направлением является начавшееся внедрение способа непрерывной разливки, предусматривающего перемещение рабочей поверхности кристаллизатора (в виде вращающихся колес, лент и др.) вместе со слитком в на-554
чальный период его формирования, что исключает трение и позволяет существенно увеличить скорость разливки (скорость движения слитка).
Еще одно перспективное и уже давно разрабатываемое направление — создание литейно-прокатных агрегатов, позволяющих сочетать непрерывную разливку с прокаткой. Непрерывным способом разливают преимущественно спокойную сталь, поскольку при разливке кипящей стали не достигается существенного увеличения выхода годного и трудно получить достаточную толщину беспузыристой корки в слитке из-за большой скорости разливки и сложности обеспечения необходимой степени окисленности металла.
Основные преимущества непрерывной разливки по сравнению с разливкой визложницы:
1) существенно повышается выход годного металла. Так, для спокойной стали получение слябов или блюмов путем непрерывной разливки вместо разливки в изложницы с последующей прокаткой обеспечивает повышение выхода годного на 10—15 % от массы разливаемой стали. Объясняется это тем, что верхняя часть каждого слитка (13—20 %) идет при прокатке в обрезь из-за наличия усадочной раковины, а при непрерывной разливке образуется одна усадочная раковина в конце разливки плавки;
2) упрощается и удешевляется производство по заводу в целом, т.к. исключаются два энергоемких этапа технологического процесса — прокатка слитков на обжимных станах (блюмингах или слябингах) и нагрев слитков до ~1100°С внагревательных колодцах перед прокаткой; при этом отпадает необходимость в блюмингах и слябингах, уменьшаются энергетические затраты, потребность в рабочей силе и площадь завода;
3) повышается качество металла, в первую очередь вследствие снижения химической неоднородности из-за более быстрого затвердевания малых по толщине слитков;
4) уменьшаются затраты ручного труда и улучшаются условия труда при разливке;
5) создаются условия для автоматизации процесса разливки.
Комплекс оборудования и механизмов для непрерывной разливки — называют установкой непрерывной разливки стали - УНРС или машиной непрерывного литья заготовок — МНЛЗ.
2. Основные типы УНРС
УНРС с вытягиванием слитка из кристаллизатора. УНРС этого типа, как отмечалось, нашли наиболее широкое применение и имеют много разновидностей. В зависимости от направления основной технологической оси установки (направления движения отливаемого слитка) различают (рис. 166) УНРС вертикального типа а, с изгибом слитка б, вертикально-радиальные в, радиальные г, криволинейные д, наклонно-криволинейные е, горизонтальные ж.
В зависимости от формы поперечного сечения отливаемого слитка различают слябовые УНРС; сортовые и блюмовые; УНРС для отливки заготовок круглого сечения; полых трубных заготовок; слитков сложного профиля, близких по сечению к готовому прокату.
Широкое промышленное применение нашли слябовые УНРС (отливка слитков плоского сечения толщиной 150—300 и шириной до 2600 мм), сортовые и блюмовые (отливка слитков квадратного сечения размером до 400x400 мм и слитков прямоугольного сечения с небольшой величиной отношения ширины к толщине (до 1,5—2,0) при толщине до 300 мм; реже применяются УНРС для отливки слитков круглого сечения диаметром до 500 мм. УНРС для отливки полых трубных заготовок и заготовок сложного профиля (например, двутаврового) находятся в стадии промышленного освоения.
В последние годы начали внедрять УНРС для отливки тонких слябов (толщиной 30—70 мм).
Рис. 166. Разновидности УНРС с вытягиванием слитка из кристаллизатора:
1 — кристаллизатор; 2 — отливаемый слиток
| В зависимости от числа одновременно отливаемых из одного сталеразливочного ковша слитков,. УНРС могут быть одно-, двух- и многоручьевыми; с увеличением числа ручьев увеличивается производительность установки. Слябовые УНРС
обычно делают двухручьевыми, сортовые и блюмовые — чаще трех-восьмиручьевыми. Разливку на УНРС ведут до израсходования металла в сталеразливочном ковше или же разливают без перерыва металл из нескольких ковшей (разливка методом "плавка на плавку").
Применяют также установки полунепрерывной разливки, на которых отливают слиток определенной длины (6-10 м). Этот слиток затем разрезают на части в холодном состоянии.
Скорость разливки, то есть скорость движения слитка при его толщине более 150 мм обычно находится в пределах от 0,5 до 1,5—2,5 м/мин, хотя на отдельных УНРС достигнуты и большие скорости; при отливке слитков малой толщины (квадрат размером менее 90x90 мм и слябы толщиной менее 70 мм) скорость разливки достигает 4—8 м/мин.
УНРС без скольжения слитка в кристаллизаторе начали применять для разливки стали в последние годы. Отсутствие скольжения обеспечивается за счет совместного движения поверхности кристаллизатора и слитка в начале его формирования, что достигается подачей жидкого металла на движущуюся охлаждаемую поверхность, выполняющую роль кристаллизатора.
Основные разновидности УНРС подобного типа: барабанные и одноленточные с подачей жидкого металла на поверхность вращающегося барабана (валка) или движущейся непрерывной ленты; двухвалковые, когда металл подают в зазор между двумя вращающимися валками; двухленточные когда металл подают в зазор между двумя движущимися непрерывными лентами (сплошными или гусеничными); барабанно-ленточные (роторные), когда металл льют в зазор между вращающимся барабаном и движущейся лентой.
УНРС последнего типа (роторные) применяют для отливки слитков с сечением, близким к прямоугольному толщиной до 160мм, остальные— для отливки полос и лент толщиной менее 10—20 мм и шириной до 800—1000 мм.
Благодаря отсутствию трения между слитком и кристаллизатором скорость движения отливаемого слитка на таких УНРС значительно выше, чем на УНРС со скольжением слитка; при отливке полос и лент толщиной менее 1—2 мм эта скорость может достигать 100—150 м/мин и более.
3. Затвердевание непрерывно вытягиваемого слитка
Принципиальная схема непрерывной разливки с вытягиванием затвердевающего слитка из кристаллизатора показана на рис. 167. В таком слитке можно выделить два участка активного охлаждения — кристаллизатор и зону вторичного охлаждения. Заливаемый в кристаллизатор металл при кон-такте с его медными водоохлаждаемыми стенками переохлаждается и затвердевает, образуя корку слитка требуемой конфигурации. На расстоянии 200—600 мм от верха кристаллизатора находится зона непосредственного контакта с коркой слитка, где теплоотвод максимальный (1,4—2,3 МВт/м2); ниже вследствие усадки корки между ней и стенками кристаллизатора возникает газовый зазор, резко снижающий теплоотвод (до 0,3—0,6 МВт/м2). В этой зоне вследствие возможной деформации непрочной корки и стенок кристаллизатора могут появляться участки плотного и неплотного контакта, в которых из-за различия в теплоотводе температура и толщина затвердевающей корки будут различаться. Эта неоднородность способствует возникновению дефектов — в местах уменьшенной толщины корки вследствие термических напряжений могут возникать продольные наружные трещины, а в переохлажденных участках плотного контакта — паукообразные поверхностные трещины.
Толщина корки на выходе из кристаллизатора должна быть достаточной, чтобы выдержать усилие вытягивания и давление жидкой стали. Эта толщина тем больше, чем больше время пребывания корки в кристаллизаторе и обычно составляет 10—25 мм, а температура поверхности 900-1250 °С.
В зоне вторичного охлаждения на поверхность движущегося слитка подают распыленную воду и устанавливают опор-Рис. 167. Схема отливки и затвердевания непрерывного слитка:
1 г- кристаллизатор; 2 — жидкий металл; 3 - затвердевший металл; 4 — опорный ролик; 5 — форсунка для подачи распьЕленной воды на слиток; 6 — тянущие
валки
ные устройства (например, ролики 4, см. рис. 167), которые предотвращают возможное выпучивание корки слитка под воздействием давления столба жидкой стали. Выбор способа охлаждения в этой зоне базировался на опыте, который показал, что при слишком интенсивной подаче охладителя (например, подаче воды струями) из-за переохлаждения поверхности слитка и возникающих при этом термических напряжений в слитке образуются внутренние и сетчатые поверхностные трещины. Поэтому применяют распыленную воду ("мягкое охлаждение"). Расход воды уменьшается по мере отдаления от кристаллизатора; его рассчитывают так, чтобы отводилось тепло, выделяющееся при кристаллизации стали, а температура корки во избежание образования трещин снижалась бы от исходной (900-1250 °С в начале зоны) не более, чем до 800-1000 °С в конце, причем в тем меньшей степени, чем выше склонность стали к трещинообразованию.
Длина зоны вторичного охлаждения составляет 80—100 % глубины лунки жидкого металла в слитке. Эту глубину (м) приближенно определяют по эмпирической формуле L = Ka\ где а — толщина отливаемого слитка, м; v — скорость вытягивания слитка, м/мин; К - коэффициент, зависящий от величины отношения ширины Ъ к толщине а слитка (при величине Ь/а, равной 1, 2, 3, 4, 6 и более, величина К соответственно составляет 240, 290, 320, 332 и 340 Мин/м2). Например, при отливке сляба сечением 300x1200 мм со скоростью 0,6 м/мин, глубина лунки составит 17,2 м, а при скорости 1,2 м/мин — 34,4 м.
Как показал опыт, продвижение фронта затвердевания в кристаллизаторе и зоне вторичного охлаждения, несмотря на нозникновение в кристаллизаторе участков неравномерности, в целом удовлетворительно подчиняется закону квадратного корня, т.е. толщину корки (см) можно определить по формуле
5 = У т или S = kv l/v ,
где т — длительность затвердевания, мин; / — расстояние от данной точки до уровня металла в кристаллизаторе, м; v — скорость разливки, м/мин; к — коэффициент затвердевания, изменяющийся от 2,3 до 3,3см/мин0,5 (величина к уменьшается при увеличении сечения слитка и зависит также от состава стали и ряда условий охлаждения).
В непрерывном слитке наблюдаются те же структурные зоны, что и при разливке в изложницы — мелкие неориентированные кристаллы у поверхности, расположенные за ними столбчатые кристаллы и различно ориентированные кристаллы в середине слитка.
& 2. УСТРОЙСТВО УСТАНОВОК НЕПРЕРЫВНОЙ РАЗЛИВКИ1. УНРС с вытягиванием и скольжением слитка
Существует несколько типов установок непрерывной разливки, основанных на вытягивании слитка из кристаллизатора с их взаимным скольжением. Широко применяемые УНРС этого типа служат в основном для отливки слябов и слитков квадратного и прямоугольного сечения. Наибольшее распространение получили установки вертикального, криволинейного и радиального типов, реже применяются вертикально-радиальные УНРС, установки с изгибом слитка, горизонтальные УНРС. В последние годы внедряют УНРС для отливки тонких слябов, разрабатываются наклонно-криволинейные установки. В зависимости от количества одновременно отливаемых слитков УНРС могут быть одно-, двух- и многоручьевыми. Вертикальные УНРС
На рис. 168 показана схема одной из вертикальных УНРС, располагаемой частично в колодце и частично в надземном сооружении. Из сталеразливочного ковша сталь поступает в промежуточный, а из него в кристаллизатор с вертикальными стенками, совершающий возвратно-поступательное движение вверх—вниз. После выхода из кристаллизатора слиток с жидкой сердцевиной движется вниз через зону вторичного охлаждения, включающую систему форсунок и опорные устройства, которые могут быть выполнены в виде роликов или брусьев и предотвращают выпучивание корки слитка.
В установке, показанной на рис. 168, верхние опорные устройства выполнены в виде расположенных вдоль слитка чугунных брусьев, по которым скользит слиток. Ниже брусьев расположены опорные вращающиеся ролики (неприводные). Для облегчения монтажа и ремонта группы брусьев или роликов объединяют общим каркасом в отдельные секции. В машинах для отливки слитков квадратного или близкого к
Рис. 168. Схема УНРС вертикального типа:
1 — сталеразливочный ковш; 2 — промежуточный ковш; 3 — кристаллизатор; 4 — опорная рама кристаллизатора; 5 — механизм качания кристаллизатора; 6 — секции опорных брусьев; 7 — механизмы прижатия и перемещения брусьев и роликов; 8 — опорная колонна; 9 — секции опорных роликов; 10 — тянущая клеть; 11 — газорезка; 12 — путь подъемной тележки; 13 — тележка для подъема слитков
квадрату прямоугольного сечения опорные устройства расположены со всех четырех сторон слитка; при отливке плоских слитков — вдоль двух широких граней слитка. В машинах для отливки плоских слитков один ряд опорных устройств закреплен жестко, а другой снабжен механизмом перемещения, что позволяет изменять толщину отливаемого слитка.
За зоной вторичного охлаждения расположена одна или две тянущие клети, которые обеспечивают вытягивание и регулирование скорости движения слитка, а также предотвращают проскальзывание слитка вниз. Каждая клеть состоит из двух или трех пар валков, соединенных с приводом и прижимаемых к слитку гидроцилиндрами.
Ниже тянущих клетей движущийся слиток разрезают на куски мерной длины с помощью газорезки. Отрезанные заготовки падают в корзину (тележку), которая, двигаясь по наклонным рельсам, поднимает заготовку до уровня пола цеха и одновременно поворачивает ее в горизонтальное положение.
Основной недостаток вертикальных УНРС — большая высота, обусловленная тем, что затвердевание слитка должно закончиться до его попадания в тянущую клеть и газорезку, а протяженность зоны затвердевания по высоте (глубина лунки жидкого металла) в непреывно отливаемом слитке очень велика. Высота крупных вертикальных УНРС достигает 40—45 м и для их размещения необходимо сооружение глубо-
ких колодцев и высоких зданий, что удорожает строительство и усложняет эксплуатацию оборудования. Другим существенным недостатком является то, что необходимость ограничивать высоту УНРС ограничивает скорость разливки (при ее росте, как следует из приводившейся на с. 559 формулы, существенно возрастает глубина лунки жидкого металла, т.е. затвердевание может не закончиться до входа слитка в тянущую клеть и зону резки).
Криволинейные и радиальные УНРС
В установках этого типа в радиальном кристаллизаторе формируется изогнутый по определенному радиусу слиток. Чтобы при последующем разгибании в слитке не образовывались трещины, радиус изгиба должен быть не менее 25-кратной толщины слитка. Обычно радиус изгиба выбирают в соответствии с соотношением R = (3(Н40)д, где а — толщина слитка, м.
В радиальных УНРС по выходе из кристаллизатора слиток движется по дуге с постоянным радиусом. После прохождения нижней точки дуги полностью затвердевший слиток разгибают, переводя его в горизонтальное положение.
В криволинейных УНРС слиток вначале движется по дуге, определяемой радиусом кривизны кристаллизатора, а затем еще в зоне вторичного охлаждения радиус кривизны дуги увеличивается, т.е. происходит постепенное разгибание слитка с жидкой сердцевиной с последующим переводом в горизонтальное положение. Рассредоточение деформации имеет целью снизить возникающие при этом в корке слитка напряжения и вероятность возникновения трещин.
Большая часть криволинейных УНРС предназначена для отливки слитков прямоугольного сечения, схема подобной машины для отливки слябов представлена на рис. 169. Жидкая сталь из сталеразливочного ковша поступает в промежуточный, а затем в радиальный кристаллизатор, снабженный механизмом качания. После выхода из кристаллизатора слиток, проходя через зону вторичного охлаждения, движется по роликовой проводке, образованной верхним и нижним рядами роликов. У узких торцевых граней ролики имеются лишь вблизи кристаллизатора. Для удобства замены при ремонтах группы соседних верхних и нижних роликов объединены в отдельные секции, где в общем каркасе смонтировано от 2
Рис. 169. Криволинейная слябовая УНРС:
1 — сталеразливочный ковш; 2 — промежуточный ковш; 3 — кристаллизатор; 4 — опорная рама кристаллизатора; 5 — механизм качания кристаллизатора; 6, 7, 9 — секции роликовой проводки (соответственно четырнадцати-, десяти- и че-тырехроликовые); 8 — опорные балки; 10 — механизм прижатия и перемещения роликов; 11 — газорезка; 12 — рольганг
до 7 пар роликов. Каждая секция опирается на фундамент, при этом нижний ряд роликов является неподвижным (базовым), а верхний снабжен пружинным или гидравлическим механизмом прижатия к слитку и механизмом перемещения, что позволяет изменять толщину отливаемого слитка.
Верхняя часть роликовой проводки предотвращает выпучивание корки слитка. Приводными, обеспечивающими движение и разгибание слитка, обычно выполняют ролики нижнего ряда. При этом ролики, расположенные вблизи кристаллизатора обычно являются неприводными, на участке с постоянным радиусом кривизны лишь некоторые ролики соединены с приводом, а на участке разгибания и выпрямления все или почти все ролики приводные. В связи с тем, что по мере увеличения толщины затвердевающей корки жесткость слитка возрастает, диаметр роликов по мере отдаления от кристаллизатора увеличивается. Так при отливке слитков толщиной 300 мм диаметр роликов от 150—200 мм у кристаллизатора возрастает до 480—600 мм на горизонтальном участке.
Машины конструируют так, что горизонтальноое движение слитка осуществляется на уровне пола цеха. На этом же участке производят резку слитка на куски мерной длины. Максимальный радиус существующих УНРС этого типа при отливке слитков толщиной до 350 мм составляет 12 м.
Основные преимущества этих машин по сравнению с вертикальными: меньшая высота, что снижает стоимость сооружения УНРС и здания цеха; возможность повышения скорости разливки, поскольку газорезку можно установить далеко от кристаллизатора и благодаря этому допустимо существенное увеличение глубины лунки жидкого металла в слитке; возможность резки слитка на куски большой длины. По этим причинам в последние годы почти отказались от сооружения вертикальных УНРС и строят преимущественно криволинейные и радиальные.
УНРС с изгибом слитка
УНРС этого типа (рис. 170, а) имеют вертикальный кристаллизатор и вертикально направленную систему вторичного охлаждения с расположенной за ней тянущей клетью, которые не отличаются от аналогичных устройств машин вертикального типа. Далее движущийся слиток изгибают, переводя в горизонтальное положение при помощи ролика, установленного за тянущей клетью. Затем слиток поступает в выпрямляющие валки, за которыми располагают газорезку. Подобные машины применяют при отливке слитков небольшой толщины (< 150 мм), поскольку при большей толщине из-за необходи-
Рис. 170. Схема УНРС с изгибом затвердевшего слитка (а) и верти кально-радиальной УНРС (б): 1 — промежуточный ковш; 2 — вер тикальный кристаллизатор; 3 - ме ханизм качания кристаллизатора; 4 — опорные ролики; 5 — тянущая клеть; 6 — изгибающий валок; 7 — слиток; 8 — тянуще-правильная клеть; 9 - газорезка; 10-12 - участки роликовой проводки соот ветственно вертикальный, изгибаю щий и радиальный; 13 — правильная "• & машина
мости иметь большой радиус изгиба не достигается заметного снижения высоты по сравнению с вертикальной УНРС.
Вертикально-радиальные УНРС
Установки подобного типа имеют (рис. 170, б) вертикальный кристаллизатор и расположенный ниже него небольшой по высоте (менее 3—4 м) вертикальный участок зоны вторичного охлаждения, включающий опорные ролики и форсунки для подачи на слиток распыленной воды. Далее расположена секция валков, изгибающих слиток с жидкой сердцевиной по дуге с определенным радиусом и затем радиальная роликовая проводка. После прохождения нижней точки дуги слиток попадает в тянуще-правильные валки, которые переводят его в горизонтальное положение, затем слиток разрезают газорезкой.
Основное достоинство этих установок по сравнению с криволинейными и радиальными — более простые в изготовлении и обслуживании прямолинейные кристаллизатор и верх зоны вторичного охлаждения, хотя общая высота установки несколько больше, чем УНРС радиального типа (на 2-4 м).
Горизонтальные УНРС
Работа большинства установок горизонтального типа основана на периодическом вытягивании слитка из неподвижного кристаллизатора.
Технологическая ось машин этого типа расположена горизонтально или наклонена на угол до 15° к горизонтали. Сталь из разливочного ковша поступает (рис. 171) в футерованный металлоприемник и далее в жестко соединенный с
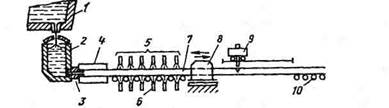
Рис. 171. Схема горизонтальной УНРС:
/ — сталеразливочный ковш; 2 — металлоприемник; 3 — огнеупорное разделительное кольцо; 4 — кристаллизатор; 5 — зона вторичного охлаждения; 6 — водяные форсунки; 7 - слиток; 8 — механизм вытягивания слитка; 9 - газорезка; 10 — рольганг
ним кристаллизатор через разделительноое кольцо 3, отверстие в котором немного меньше размера полости кристаллизатора. Разделительное кольцо должно быть стойким против тепловых ударов и размывания потоком металла, быть малотеплопроводным, чтобы здесь не застывала сталь, и к нему не должен прилипать затвердевающий металл; чаше разделительное кольцо делают из нитрида бора.
После кристаллизатора затвердевший по периферии слиток попадает в зону вторичного охлаждения, которая представляет собой рольганг с системой водяных форсунок; опорные устройства обычно отсутствуют, поскольку из-за малого ферростатического давления выпучивание корки слитка не происходит. Далее расположен механизм периодического вытягивания слитка. Механизм перемещает слиток вперед на 10—50 мм, затем возвращается назад, после чего цикл повторяется; во время обратного движения механизма слиток остается неподвижным, либо несколько осаживается назад. Число циклов изменяется от 20 до 200 в минуту. Периодическое вытягивание слитка заменяет качание кристаллизатора, используемое на вертикальных и криволинейных машинах для предотвращения зависания и разрывов корки слитка в кристаллизаторе. За механизмом вытягивания расположена газорезка и рольганг с приводными роликами для транспортировки отрезанных заготовок на склад.
Горизонтальные УНРС применяют для отливки сортовых слитков квадратного сечения и прямоугольного сечения, близкого к квадратному толщиной до 200 мм и круглых заготовок диаметром до 330 мм; скорость разливки 4м/мин.
Горизонтальные УНРС из-за малой высоты вписываются в габариты любого цеха и предназначены црежде всего для установки в существующих цехах при замене разливки в изложницы на непрерывную разливку. Помимо возможности размещения в существующих цехах достоинства горизонтальных УНРС: небольшие капитальные затраты вследствие малой высоты и меньшего количества оборудования; свободный доступ персонала ко всем узлам УНРС вследствие их размещения на уровне пола цеха; отсутствие необходимости регулировать расход металла в кристаллизатор, поскольку он определяется скоростью вытягивания слитка; удаление поверхности жидкого металла из кристаллизатора, что исключает в слитке дефекты из-за окисления и охлаждения поверхности металла. 566
УНРС для отливки тонких слябов
Большинство существующих слябовых УНРС служат для отливки плоских слитков толщиной 200-300 мм, которые в последующем прокатывают на лист. В последние годы в связи с необходимостью повышения экономичности производства пришли к выводу о целесообразности отливки значительно более тонких заготовок, для прокатки которых требуются менее мощные станы, что значительно снижает энергозатраты и другие издержки. Начата эксплуатация и сооружают новые УНРС для получения слябов толщиной от 30—40 до 70-80 мм.
УНРС для отливки тонких слябов — это в большинстве случаев установки с изгибом слитка, т.е. они имеют вертикальные кристаллизатор и зону вторичного охлаждения и за ними изгибающий ролик, после которого слиток движется по дуге, попадая в выпрямляющие валки. Далее выпрямленный слиток движется в горизонтальном направлении и его разрезают на куски мерной длины.
Проблема создания подобных установок связана в основном с трудностью осуществления подвода жидкого металла в кристаллизатор, поскольку диаметр погружного разливочного стакана превышает ширину полости кристаллизатора. Решают эту проблему двумя способами. Одна разновидность УНРС предусматривает применение тонких плоского сечения погружных стаканов ("щелевидных" стаканов); в УНРС другого типа применяют "воронкообразные" кристаллизаторы. Такой кристаллизатор имеет в нижней части плоские параллельные широкие стенки, формирующие тонкий плоский слиток, а в середине верхней части имеется воронкообразное расширение, куда входит плоский погружной стакан (см. рис. 181). Формирующаяся в верхней воронкообразной части кристаллизатора оболочка слитка при его вытягивании деформируется и слиток приобретает в нижней части кристаллизатора прямоугольное сечение.
УНРС для отливки тонких слябов подразделяют также на две следующие разновидности: установки, у которых сечение выходящего из кристаллизатора слитка остается неизменным, и установки, у которых слиток с жидкой сердцевиной подвергают обжатию, уменьшая его толщину.
Кроме того, в Германии разработана конструкция УНРС с вертикально-радиальным кристаллизатором, у которой для
облегчения ввода погружного стакана широкие стенки кристаллизатора в верхней его части расположены вертикально, а ниже они изогнуты по дуге, формируя изогнутый слиток, движущийся далее по радиальной роликовой проводке с последующим выпрямлением и переводом в горизонтальное положение, причем на радиальном участке слиток подвергают обжатию.
Скорость разливки на УНРС для отливки тонких слябов достигает 4—6,5 м/мин.
Наклонно-криволинейные УНРС
Установки подобного типа разработаны недавно и ведется отработка технологии разливки на таких УНРС и совершенствование их отдельных узлов. По устройству такие УНРС схожи с криволинейными и отличаются от обычных криволинейных тем, что дугообразный кристаллизатор установлен (см. рис. 166, е) наклонно, т.е. так, что его условная продольная ось наклонена на угол 40-45° к горизонтали. После выхода из кристаллизатора движущийся слиток разгибают в нескольких точках, переводя в горизонтальное положение.
Благодаря наклонному расположению кристаллизатора такие УНРС имеют (рис. 166, е) значительно меньшую высоту, чем обычные криволинейные и считаются перспективными для установки в существующих сталеплавильных цехах при внедрении непрерывной разливки вместо разливки стали в изложницы.
Основные узлы УНРС
Ниже описаны основные узлы, используемые на широко распространенных УНРС с вытягиванием слитка из кристаллизатора.
Промежуточный ковш, обеспечивающий подвод жидкого металла из сталеразливочного ковша в кристаллизатор— это ковш небольшой (менее 1,6 м) высоты с одним, а на многоручьевых УНРС с несколькими разливочными стаканами, как правило, имеющими стопора; ковш вмеещает от 8—10 до 15 % массы металла в сталеразливочном ковше. Помимо подвода жидкого металла в кристаллизатор промежуточный ковш обеспечивает постоянство условий подачи металла в кристаллизатор в течение всей разливки, т.е. одинаковый и небольшой напор струи металла, поступающего в кристаллизатор
(за счет поддержания в ковшв| постоянного уровня металла высотой 0,6—1,2 м); регулирование стопором скорости подачи металла в кристаллизатор; подачу металла в несколько кристаллизаторов на многоручьевых УНРС; разливку по методу "плавка на плавку" (запас металла в промежуточном ковше позволяет продолжать разливку в периоды, когда опорожненный сталеразливочный ковш заменяют новым).
На сортовых УНРС для отливки слитков малого сечения (менее 125x125 мм) иногда применяют промежуточные ковши со стаканами-дозаторами без стопоров. Постоянство уровня металла в кристаллизаторе поддерживают при этом изменением скорости вытягивания слитка из кристаллизатора (скорости разливки).
Промежуточный ковш по устройству схож с аналогичными ковшами для разливки стали в изложницы (см. рис. 159); в поперечном сечении промежуточные ковши чаще всего имеют форму вытянутого прямоугольника, чтобы обеспечить на многоручьевых УНРС подачу металла в несколько кристаллизаторов, обычно располагаемых в одну линию. Футеровка ковша имеет арматурный слой из шамотного кирпича и рабочий слой из шамотного кирпича или из огнеупорной массы (набивной, наливной, либо нанесенной путем торкретирования). Рабочий слой заменяют после разливки одной—пяти плавок.
Для снижения теплопотерь ковши накрывают футерованными крышками, а до начала разливки футеровку прогревают до температуры 900-1200 °С.
Кристаллизатор является важнейшим конструктивным элементом УНРС; он должен обеспечить быстрое формирование достаточно толстой и прочной корки слитка без дефектов. Для обеспечения этого и предотвращения расплавления самого кристаллизатора при подаче в него жидкой стали, стенки кристаллизаторов делают водоохлаждаемыми, а внутреннюю их часть, соприкасающуюся с жидким металлом, выполняют из меди. Медь, несмотря на ее легкоплавкость (температура плавления 1083 °С) и невысокую твердость и прочность, применяют потому, что благодаря высокой теплопроводности она быстро передает тепло охлаждающей воде и даже при контакте с жидкой сталью не перегревается и сохраняет прочность.
Применяют кристаллизаторы трех типов: блочные, гильзовые и составные. Блочные кристаллизаторы делают из ко-
ваного или литого медного блока, толщина их стенок составляет 150—175 мм. В стенках блока сверлят продольные отверстия для охлаждающей воды. Гильзовые кристаллизаторы делают из медной гильзы (трубы) с толщиной стенки 6—20 мм, которую закрепляют в наружном стальном кожухе. Охлаждающая вода проходит по узкой (около 5 мм) щели между медной и стальной стенками со скоростью 6—7,5 м/с. Блочные и гильзовые кристаллизаторы применяют для отливки слитков небольшого сечения (менее 200x200 мм).
Рис. 172. Составной кристаллизатор с петлевой системой охлаждения для отливки плоских слитков:
| Наибольшее распространение получили составные (сборные) кристаллизаторы, которые выполняют из четырех отдельных стенок, скрепленных в одно целое с помощью специальных стяжных устройств. Общий вид одной из разновидностей подобных кристаллизаторов показан на рис. 172 (кристаллизатор для отливки слитков плоского сечения). Каждая стенка составного кристаллизатора состоит из медной и стальной пластин (плит), скрепленных друг с другом с помощью шпилек. Медная плита обеспечивает быстрый теп-лоотвод, стальная — придает стенке прочность и при больших размерах плиты ее делают литой с ребрами жесткости (рис. 172, 11).

Составные кристаллизаторы подразделяют на тонкостенные и толстостенные. Первые (рис. 173, а) имеют медную пластину толщиной 10—20 мм, причем в медной или стальной пластине вырезаны продольные канавки для охлаждающей воды так, что вода в них движется между медной и стальной пластинами. Недостаток таких кристаллизаторов в том, что в результате напряжений, возникающих из-за разности температур жидкой стали и охлаждающей воды, медные пластины малой толщины сравнительно легко коробятся, что вызывает их усиленный износ вытягиваемым слитком и неравномерное прилегание различных участков стенок кристаллизатора к поверхности слитка. Последнее способствует возникновению поверхностных трещин (продольных, паукообразных и иногда поперечных) и ужимин на слитке. По этой причине применяют в основном толстостенные кристаллизаторы, имеющие медные плиты толщиной 50—100 мм, в которых просверлены (см. рис. 173, б) круглые продольные каналы для охлаждающей воды обычно диаметром 20 мм. Благодаря меньшему короблению толстых медных плит стойкость толстостенных кристаллизаторов значительно выше, чем тонкостенных и снижается пораженность слитка поверхностными дефектами.
Форма поперечного сечения внутренней полости кристаллизатора определяется сечением отливаемого слитка. Высоту кристаллизатора выбирают такой, чтобы за время пребывания в нем металла успела сформироваться достаточно прочная (толщиной 10—25 мм) наружная оболочка слитка; эта высота составляет 0,7—1,2 м. Внутреннюю рабочую поверхность сте-
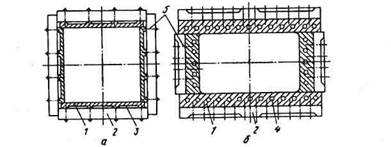
1 — стяжной болт; 2 и 3 — ось и сухарь для регулирования положения узкой стенки; 4 — стальная плита; 5 — водоподводящий коллектор; 6 — направление движения воды; 7 — каналы для воды в медных плитах; 8 — каналы для воды в стальных плитах; 9 — медная плита; 10 — слив воды; 11 — ребра жесткости; 12 — опора кристаллизатора на раму механизма качания
Рис. 173. Поперечное сечение составных кристаллизаторов — тонкостенного (а) и толстостенного (ff):
/ — медная плита; 2 — стальная плита; 3 — канавка для воды; 4 — сверленый канал для воды; 5 — шпильки
нок кристаллизаторов изготовляют гладкой или волнистой. Волнистая поверхность снижает пораженность слитка продольными трещинами.
Из-за малой твердости и прочности меди внутренняя поверхность стенок кристаллизатора сравнительно быстро изнашивается и повреждается в результате трения о поверхность вытягиваемого слитка. Поэтому составные кристаллизаторы после разливки 40—70 плавок разбирают и поврежденный рабочий слой стенок сострагивают, после чего кристаллизатор собирают и вновь эксплуатируют. Такую операцию повторяют до трех—пяти раз за время службы медной стенки, что позволяет уменьшить расход меди. С целью повышения износостойкости все шире применяют покрытие рабочей поверхности медных стенок тонким слоем более износостойких материалов; в частности, находят применение хромовое, никелевое, железоникелевое, железоникельвольфра-мовое и другие покрытия. Покрытия имеют толщину от 0,15 до 1мм, их наносят гальваническим методом, напылением, наплавкой и другими способами. Кроме того, для изготовления стенок кристаллизаторов пробуют применять сплавы на основе меди, обладающие более высокой износостойкостью (сплавы содержащие до 0,1—2,5 % серебра, хрома, кобальта, никеля и др.).
Применяют кристаллизаторы с прямоточной и петлевой системами охлаждения. В первом случае воду подводят отдельно к каждой из четырех стенок, по каналам которой она движется снизу вверх; после чего уходит на слив. При петлевой системе, применяемой в кристаллизаторах прямоугольного сечения, вода проходит по каналам стенок дважды; вначале (см. рис. 172) по каналам торцевых стенок и краям широких она движется сверху вниз, а затем по каналам средней части широких стенок — вверх. Петлевая система позволяет снизить расход воды примерно в дна раза.
Подвод и отвод воды к каналам медных стенок осуществляют либо по кольцевым трубам, охватывающим верх и низ кристаллизатора, либо по каналам в стальных плитах (см. рис. 172). Скорость воды в каналах кристаллизатора должна быть не менее 5 м/с, температура отходящей воды не выше 40 °С; расход воды составляет около 90 м3/ч на 1м периметра полости кристаллизатора, при прямоточном охлаждении.
Конструкция кристаллизаторов непрерывно совершенствуется. Так созданы и начали применяться регулируемые кристаллизаторы, позволяющие изменять по ходу разливки ширину отливаемого плоского слитка за счет автоматического перемещения узких стенок между широкими с помощью электромеханического или гидравлического привода. Получают распространение комбинированные УНРС, позволяющие отливать через один кристаллизатор либо плоский слиток большой ширины, либо два слитка меньшей ширины; это достигается за счет установки в кристаллизаторе водоохлажда-емой перегородки, которая разделяет полость кристаллизатора на две половины, в каждую из которых подают металл через отдельный разливочный стакан (например, можно отливать один слиток плоского сечения шириной 2700 мм или два слитка шириной по 1300 мм).
За рубежом начали применять кристаллизаторы со спрей-ерным (струйным) охлаждением стенок. Такой кристаллизатор представляет собой тонкостенную медную гильзу, закрепленную в стальной камере,. внутри которой размещены рядами форсунки, подающие струи воды на всю поверхность медной гильзы.
Механизм качания кристаллизатора обеспечивает в течение всей разливки возвратно-поступательное движение кристаллизатора вверх-вниз, т.е. вдоль отливаемого слитка, что необходимо для предотвращения отрыва верхней тонкой части корки от движущегося слитка вследствие трения о стенки кристаллизатора. В случае отрыва верхняя часть корки зависает на стенках кристаллизатора, а место разрыва движется с остальной частью слитка вниз, и после его выхода из кристаллизатора происходит вытекание жидкого металла в зону вторичного охлаждения (прорыв металла под кристаллизатором) с аварийной остановкой разливки. Подобные "зависания" и "прорывы" постоянно наблюдались в годы освоения непрерывной разливки, когда кристаллизаторы устанавливали неподвижно. Положительное воздействие внедренного позднее возвратно-поступательного движения объясняется следующим: в период совместного движения кристаллизатора и слитка вниз трение между ними отсутствует и затвердевающая корка слитка утолщается и упрочняется так, что при последующем движении кристаллизатора вверх она не разрывается. В то же время при движении вверх становятся
| | | | | | | | | |
| доступными для смазки те участки поверхности стенок кристаллизатора, которые в момент его движения вниз оказываются залитыми жидким металлом; смазка же уменьшает трение и тем самым также снижает возможность разрыва и зависания корки слитка.
Движение кристаллизатора вверх и вниз чаше всего осуществляют по синусоидальному закону, величина шага качания изменяется в пределах 3 — 20 мм, частота от 40 до 200-300 циклов в минуту, обычно при увеличении скорости частоту качания увеличивают.
Существует несколько типов механизмов качания кристаллизаторов. На криволинейных УНРС наибольшее применение получил механизм параллелограммного типа, схематически показанный на рис. 174. Криволинейный кристаллизатор 1 закреплен в раме 2, опирающейся на рычаги 5 и 3 механизма качания. Вращаемый с помощью электродвигателя кривошип 7 обеспечивает перемещение шатуна б по направлению стрелок "А" и тем самым качание рычага 5 вокруг оси 4. Воздействие качающегося рычага в сочетании с рычагом 3 вызывает перемещение рамы с кристаллизатором вверх-вниз по траектории дуги с радиусом R. Изменяя число оборотов двигателя, регулируют частоту качания кристаллизатора, а изменяя величину радиуса кривошипа — величину амплитуды качания.
Зона вторичного охлаждения представляет собой располагаемую ниже кристаллизатора часть УНРС, где на поверхность движущегося слитка подают охлаждающую среду. Как уже отмечалось, в этой зоне от слитка должно отбираться тепло, выделяющееся при кристаллизации жидкого металла, а поверхность слитка не должна охлаждаться ниже 800—1000 °С. Чтобы достичь этого применяют "мягкое" охлаждение (распыленной водой, водовоздушной смесью), рас-средотачивая его на большое расстояние по длине слитка (на 70—90 % протяженности жидкой фазы, т.е. металлургической длины УНРС).
Оборудование зоны вторичного охлаждения состоит из охлаждающих и опорных устройств; обычно эта зона заключена в герметичный кожух, необходимый для улавливания пара, образующегося при испарении подаваемой на горячий слиток воды. Охлаждающие устройства при водяной системе охлаждения (рис. 175) представляет собой систему трубопроводов с запорными и регулирующими устройствами и многочисленными
Рис. 174. Механизм качания кристаллизатора
Рис. 175. Секция вторичного охлаждения криволинейной УНРС:
1 - слиток; 2 - опорный ролик; 3 — форсунка; 4 — трубчатый коллектор; 5 — задвижка
форсунками, распыливающими подаваемую на слиток воду. В последние годы начали применять водовоздушное охлаждение, т.е. подачу через распыливающие форсунки водовоздушной смеси; в этом случае к форсункам помимо воды подводят сжатый воздух, либо перед форсунками устанавливают смесители воды и воздуха. Это охлаждение по сравнению с водяным имеет ряд преимуществ: более тонко распыливается вода, более равномерно распределяются водяные капли в выходящем из форсунки "факеле" и он орошает большую площадь поверхности слитка, что делает охлаждение более "мягким", снижая неравномерность температур поверхности слитка и пораженность слитка поверхностными трещинами; расширяется диапазон регулирования интенсивности охлаждения за счет возможности изменения соотношения воды и воздуха в смеси; снижается расход воды на вторичное охлаждение.
Форсунки располагают между опорными роликами (рис. 175) или брусьями в один, два, три ряда вдоль направления движения слитка в зависимости от его ширины. При отливке плоских слитков охлаждают широкие грани; у узких граней форсунки устанавливают лишь под кристаллизатором.
Интенсивность охлаждения должна уменьшаться по мере удаления слитка от кристаллизатора. С тем, чтобы обеспечить постепенное снижение расхода воды, зону вторичного охлаждения делят по длине на несколько (до восьми) секций, объединяющих группу форсунок и имеющих самостоятельный подвод воды. Регулирование расхода воды по секциям в зависимости от скорости разливки, температуры поверхности слитка и иногда других параметров производят автоматически в соответствии с разработанными для этих случаев режимами. Обычно длину секций вторичного охлаждения делают равной длине роликовых секций УНРС.
Опорные устройства системы вторичного охлаждения предназначены для предотвращения деформации (выпучивания) тонкой затвердевшей корки слитка под воздействием давления вышележащих слоев жидкой стали, находящейся в центральной, незатвердевшей части слитка. В вертикальных УНРС и установках с изгибом слитка (рис. 168 и 170, а) опорные устройства выполняют в виде системы вращающихся неприводных опорных роликов. На некоторых вертикальных УНРС (рис. 168) в верхней части зоны вторичного охлаждения вместо опорных роликов устанавливают более прочную систему продольных чугунных брусьев, по которым скользит поверхность движущегося слитка.
В УНРС с криволинейной осью опорные устройства представляют собой ролики, образующие роликовую проводку, ^внутри которой движется слиток.
Опорные устройства выполняют так, что расстояние между рядами роликов и брусьев можно изменять; это позволяет быстро перестраивать УНРС при отливке слитков разной толщины. В УНРС криволинейного типа нижний ряд роликов является базовым, а верхний можно перемещать
Тянущие устройства. В вертикальных УНРС это устройство располагают ниже зоны вторичного охлаждения; оно представляет собой одну-две тянущих клети, каждая из которых включает закрепленные в одной станине две или три (рис. 168) пары валков, соединенных с приводом и прижимаемых к слитку с помощью гидроцилиндров. В УНРС с изгибом слитка имеется два тянущих устройства — тянущая клеть в конце вертикального участка установки и тянуще-правильные ролики, обеспечивающие выпрямление слитка и его дальнейшее перемещение в горизонтальном направлении (рис.170,а).
В слябовых криволинейных и радиальных УНРС движение слитка обеспечивают снабженные приводом (приводные) ролики роликовой проводки; последняя обычно выполнена из нескольких секций, объединяющих в одном каркасе от двух до семи пар роликов (см. рис. 169). При этом верхняя часть проводки (до 2,5-3,5 м от уровня металла в кристаллизаторе) является неприводной, а далее следует приводная часть проводки. В ней число приводных роликов в секциях увеличивается по мере отдаления от кристаллизатора, а на участке перевода движения слитка в движение по горизонтали все ролики делают приводными. На некоторых радиальных УНРС в месте разгибания слитка имеется правильно-тянущая машина, выделенная в отдельный блок часть приводной роликовой проводки.
У сортовых радиальных УНРС в большинстве случаев роликовые проводки являются неприводными, а на участке разгибания слитка располагают тянуще-правильную машину, которая выпрямляет и тянет слиток.
Необходимое усилие прижатия приводных роликов к слитку на разных УНРС, обеспечивают с помощью гидроцилиндров или пружинно-винтовым устройством.
Затравка предназначена для образования временного дна в кристаллизаторе перед началом разливки и для вытягивания первых метров отливаемого слитка. На вертикальных и горизонтальных УНРС затравка представляет собой металлическую штангу такого же сечения, что и отливаемый слиток. На криволинейных установках применяют гибкие (цепные) затравки из шарнирно соединенных звеньев; на радиальных УНРС— как цепные, так и жесткие в виде дугообразного бруса по форме сечения одинакового со слитком. Затравки цепного типа могут быть с жесткими звеньями постоянной толщины и звеньями изменяемой толщины (надувные). В надувной затравке каждое звено состоит из корпуса и подвижной крышки (пластины), между которыми по всей длине затравки проложены резинотканевые рукава; при подаче в рукава сжатого воздуха крышки приподнимаются и толщина звеньев и затравки увеличивается до необходимой величины, определяемой расстоянием между роликами.
Затравка снабжена головкой, в котороой имеется углубление в виде "ласточкиного хвоста" или Г-образной формы (рис. 176); сечение головки затравки соответствует сече-
37-3810
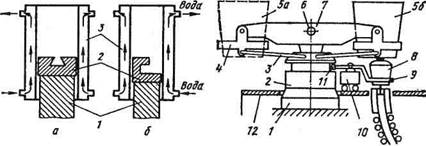
Рис. 176. Затравка в кристаллизаторе перед началом разливки:
а — с головкой, имеющей паз в виде ласточкиного хвоста; б — с Г-образной
головкой; 1 — затравка; 2 — головка затравки; 3 — кристаллизатор
Рис. 177. Повторный стенд УНРС:
1 — опорная станина; 2 — поворотная платформа; 3 — тяга; 4 — подвеска; 5, а и 5, б — сталеразливочный ковш; б — ось крепления консоли; 7 — консоль; 8 — промежуточный ковш; Р — несущая рама тележки; 10 — тележка; 11 — опорные ролики; 12 — рабочая площадка УНРС
нию отливаемого слитка. Перед началом разливки затравку вводят в кристаллизатор и ее головка образует временное дно, а низ затравки находится в тянущих валках. Заливаемый в кристаллизатор металл застывает в углублении головки, обеспечивая сцепление затравки со слитком. При включении тянущих валков затравка начинает двигаться вниз и тянет за собой слиток. После выхода затравки из тянущих валков ее отделяют от слитка.
Устройство для резки слитка на куски определенной длины (заготовки) представляет собой газорезку и реже гидравлические ножницы. Газорезка — это подвижная тележка, снабженная двумя газокислородными резаками, которые при резке перемещаются поперек слитка, а сама газорезка при этом движется вместе со слитком, сцепляясь с ним перед началом резки пневматическими захватами. Иногда синхронизацию перемещения газорезки со слитком осуществляют электрорегулирующим устройством. После окончания резки газорезка возвращается в исходное положение, после чего цикл повторяется. Недостатком газовой резки являются потери металла, превращающегося в месте резки в окалину.
Оборудование для быстрой смены ковшей. Современные УНРС оборудуют поворотными и иногда передвижными стендами, которые удерживают во время разливки сталеразливочный
ковш над промежуточным и обеспечивают быструю замену ковшей при разливке методом "плавка на плавку". Поворотный стенд (рис. 177) имеет располагаемую на основании 1 поворотную платформу 2, на которую через ось 6 опирается консоль 7. В подвесках 4 консоли можно установить два ковша; нертикальное перемещение ковша достигают качанием консоли, при этом тяга 3 обеспечивает плоскопараллельное движение подвесок и ковшей. При разливке методом "плавка на плавку" после опорожнения ковша 56 стенд поворачивают на 180°, устанавливая тем самым второй ковш 5а над промежуточным, и тотчас начинают подачу металла из второго ковша в промежуточный. Разливка во время поворота стенда продолжается за счет расходования металла, имевшегося в промежуточном ковше.
Для замены промежуточных ковшей в сочетании с поворотными стендами применяют тележки, перемещаемые под стендом ПО прямолинейному или кольцевому рельсовому пути. Тележка нторого типа (см. рис. 177) имеет нижние приводные колеса и верхние неприводные 11, опирающиеся на основание поворотного стенда. Промежуточный ковш устанавливают на несущей раме 9 тележки и для его замены передвигают тележку, подавая на ее место вторую с новым промежуточным ковшом; подачу металла в кристаллизатор при этом прекращают на 1—2 мин.
2. УНРС без скольжения слитка в кристаллизаторе
Работа и устройство УНРС этого типа, как отмечалось ранее, основана на том, что рабочая поверхность кристаллизатора перемещается вместе со слитком в начальный момент его формирования; это исключает их взаимное скольжение и возникновение при этом сил трения между слитком и кристаллизатором. Благодаря отсутствию трения эти УНРС позволяют отливать слитки значительно меньшей толщины и при значительно больших скоростях, чем традиционные УНРС с вытягиванием слитка из кристаллизатора.
Опробованы и внедряются либо эксплуатируются несколько разновидностей УНРС этого типа: двухвалковые; барабанные с ограничительным роликом или без него; одно- и двухлен-точные со сплошными или гусеничными лентами (все служат для отливки полос и лент толщиной от 10—20 до долей мил-
лиметра) и барабанно-ленточные или роторные (для отливки слитков с сечением, близким к прямоугольному толщиной до 160 мм).
Сооружение и эксплуатация таких УНРС обходится значительно дешевле, чем традиционных; со скольжением слитка в кристаллизаторе; кроме того снижаются энергозатраты при дальнейшей прокатке, так как для прокатки тонких заготовок требуются станы небольшой мощности.
Двухвалковые УНРС используют для получения плоских слитков (полос, лент). В таких установках (рис. 178, а) жидкий металл из промежуточного ковша подают сверху в зазор между двумя параллельными вращающимися навстречу друг другу охлаждаемыми валками (роликами); в торцах валков расположены поперечные пластины (плиты), ограничивающие литейное пространство с боков. Между валками образуется (рис. 178, а) сужающаяся книзу воронка из жидкого металла; в верхней ее части на поверхности валков формируется наружная корочка слитка, которая в дальнейшем подвергает-
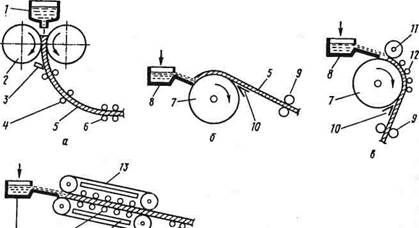
8 12 14 12
г
Рис. 178. УНРС без скольжения слитка в кристаллизаторе:
а — двухвалковая; б — барабанного типа без ограничительного ролика; в — барабанного типа с ограничительным роликом; г — двухленточная; 1 — промежуточный ковш; 2 — охлаждаемый валок; 3 — изгибающее устройство; 4 — направляющие ролики; 5 — слиток; б — выпрямляющие ролики; 7 — охлаждаемый барабан; 8 — желоб; 9 — тянущие валки; 10 — снимающий клин; 11 — ограничительный ролик; 12 — опорные ролики; 13 — лента; 14 — охладитель ленты
ся обжатию вследствие сближения поверхностей вращающихся налков. Таким образом, валки выполняют роль кристаллизатора и одновременно производят обжатие слитка. После выхода из валков слиток с помощью изгибающего устройства 3 и системы роликов плавно переводят в горизонтальное положение.
Жидкий металл в зазор между валками необходимо подавать равномерно по ширине отливаемого слитка; подачу металла ведут открытыми струями через желоб или под уровень металла погружными стаканами (плоские стаканы с щелевид-ным выходным отверстием или несколькими круглыми отверстиями).
На УНРС подобного типа с диаметром валков 1200 мм при толщине плоского отливаемого слитка 1—5 мм скорость его движения составляет 20—100 м/мин; ширина отливаемого слитка достигает 800 мм. Недостатком таких УНРС являются малое время контакта корочки слитка с валками и возможность образования поверхностных трещин при деформации тонкой формирующейся оболочки слитка.
УНРС барабанного типа служат для отливки полос и лент. В этих установках жидкий металл подают на поверхность вращающегося вокруг горизонтальной оси охлаждаемого барабана. Разработано две разновидности таких УНРС: с ограничительным роликом (рис. 178, в) и без него (рис 178, б). i рабан диаметром до 1м полый, его рабочая поверхность из стального листа охлаждается водой изнутри, что обеспечивает охлаждение нижней поверхности отливаемой полосы; верхнюю наружную поверхность полосы иногда охлаждают водой, распыляемой форсунками, либо потоком инертного газа.
Для увеличения протяженности зоньи контакта полосы с барабаном некоторые УНРС помимо ограничительного ролика снабжены опорными роликами 12 (рис. 178, в). Отливаемая полоса отделяется от барабана с помощью снимающего клина. После отделения от барабана полоса попадает в тянущие ролики и затем на моталку, сматывающую полосу в рулон.
Жидкий металл подают как на восходящую, так и нисходящую поверхность вращающегося барабана; при этом должно обеспечиваться его равномерное поступление по всей ширине барабана. На установках без ограничительного ролика толщина отливаемой ленты (полосы) определяется скоростью вращения барабана и количеством подаваемого на поверх-
ность барабана расплава. При этом для получения постоянной толщины ленты необходимы стабильность свойств расплава (температура, жидкотекучесть и др.) и надежные системы автоматического контроля и управления разливкой. Более перспективными считаются установки с ограничительным роликом, у кооторых постоянство толщины и гладкая поверхность ленты обеспечиваются за счет воздействия этого ролика. Толщина отливаемых полос и лент составляет от 20 до долей миллиметра, ширина достигает 1000 мм, скорость разливки 10—бОм/мин и более.
Ленточные УНРС, служащие для отливки тонких полос, могут быть одно- и двухленточными. Двухленточная установка (рис. 178, г) имеет две располагаемые наклонно параллельные бесконечные ленты, движущиеся с одинаковой скоростью. Ленты могут быть гусеничными или сплошными из стали. С внутренней стороны ленты охлаждаются водой; прижатие ленты к отливаемой полосе обеспечивают опорные ролики 12. Продольное расширение ленты вследствие ее нагрева компенсируют натягивающими роликами.
Металл в зазор между лентами подают либо через желоб, либо плоскими погружными стаканами.
На одной из подобных установок со сплошными лентами (установка "Хезелетт" в США) отливают полосы толщиной 20— 80 мм при скорости разливки от 4—6 до 15 м/мин.
Роторные или барабанно-ленточные УНРС применяют, как правило, для отливки слитков трапециевидного (близкого к прямоугольному) сечения. Одна из таких УНРС, входящая в состав литейно-прокатного агрегата, показана на рис. 179. Жидкий металл поступает из промежуточного ковша сверху в зазор между вращающимся литейным колесом и движущейся лентой. Литейное колесо 7 диаметром 3 м из стали имеет закрепленный на ободе медный водоохлаждаемый канал, имеющий форму расширяющейся кверху трапеции, что облегчает выход слитка из канала в процессе разливки (размеры сечения канала 160x130x128 мм). Бесконечная стальная лента толщиной 1,6 мм прижимается к ободу колеса двумя валками 4, а третий приводной валок 3 обеспечивает ее натяжение и непрерывное движение. Движущаяся лента прижимается к ободу колеса, образуя кристаллизатор длиной 1,8 м, в котором отсутствует скольжение слитка. В зоне контакта с колесом ленту снаружи охлаждают.
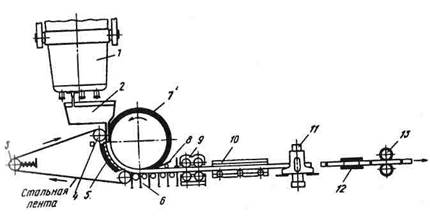
Рис. 179. Литейно-прокатный агрегат с роторной УНРС: I — сталсразливочный ковш; 2 — промежуточный ковш; 3 — приводной валок; 4 -прижимные валки; 5 — охлаждение ленты; 6 — направляющие ролики; 7 — литейное колесо; 8 — снимающий клин; 9 — тянущие ролики; 10 — печь для выравнивания температуры слитка; 11 — ножницы; 12 — вертикальная прокатная клеть; 13 — горизонтальная прокатная клеть
В нижней части колеса слиток выводят из трапециевидного канала и плавно разгибают с помощью водоохлаждаемого клина и ряда роликов, после чего он поступает в тянущую клеть. Скорость разливки (скорость движения слитка) на таких УНРС достигает 4-6 м/мин. 3. Литейно-прокатные агрегаты
Совмещение непрерывной разливки с прокаткой, т.е. прокатка горячего слитка после выхода из УНРС, позволяет исключить операцию нагрева металла перед прокаткой и, тем самым, заметно снизить уровень энергозатрат. Поэтому в течение многих лет ведутся работы по созданию литейно-ирокатных агрегатов (ЛПА), объединяющих УНРС и прокатный стан. Основная трудность при этом связана с тем, что скорость движения слитка на высокопроизводительных УНРС со скольжением слитка в кристаллизаторе в несколько раз ниже скорости движения прокатываемой заготовки на прокатных станах. Сочетание УНРС с прокатным станом облегчается при разливке стали на начинающих применяться в последние годы установках без скольжения слитка в кристаллизаторе, обеспечивающих значительно большие скорости разливки, чем традиционные УНРС.
Поиск по сайту:
|